An informational blog dedicated to the application of industrial controls, valves and valve automation in the municipal, environmental and industrial markets. This resource will provide educational information in the form of new product introductions, application notes, and basic concepts of all things related to instrumentation, process control, industrial valves, valve actuation, and flow control. Courtesy of Automatic Controls of Virginia (ACVA).
Happy Holidays from Automatic Controls of Virginia
"This is my wish for you: peace of mind, prosperity through the year, happiness that multiplies, health for you and yours, fun around every corner, energy to chase your dreams, joy to fill your holidays!" D.M. Dellinger
The Val-Matic Quadrosphere Forged Ball Valve Ring Master Seating
The Val-Matic Quadrosphere forged ball valve is a proven unique trunnion mounted ball valve design for long life in numerous industrial applications where fluids with sediment tends to clog and damage traditional ball valves. The ball is not spherical, as in a typical ball valve. Surfaces of the ball are contoured with recessed surfaces on four sides of the ball. The contoured recess surfaces provide for extra flow paths and also provide lift edges that wipe the body seat clean during opening and closing. The hard chrome plated stainless steel ball provides low friction and abrasion resistance. The recessed surfaces provide multiple flow paths for particulates to be flushed from the body during every operation, thereby providing a self-cleaning valve.
The valve is equipped with a seat on both ends to provide bi-directional seating. The seating is available in double block and bleed (DBB) or double isolation and bleed (DIB) depending on the application. As with all trunnion mounted ball valves, when line pressure is applied to the valve, fluid flows behind the seat ring and presses the seat ring and resilient seal insert against the ball to make a tight seal. The ball is directly anchored to the body by rigid trunnions. The ball will rotate 90 degrees during opening and closing but the trunnions prevent any axial motion of the ball during pressurization. The valve stem is equipped with a shoulder to prevent blowout during process operations. The stem is sealed with o-rings and graphite packing for low fugitive emissions and fire safe applications. An emergency injection fitting is provided for emergency sealing until maintenance can be performed.
For applications like geothermal fluid where scale and sediment are present in high concentrations, the optional ring master seat is used. The ring master uses an external pressure source such as grease or gas to press the seat to insert against the ball. Since the injection pressure is greater than the line pressure, the seat ring pocket is always isolated from the process fluid and cannot collect sediment over time. One method of applying external pressure to the seat is with a pressurized accumulator assembly. Grease or other compatible fluid is injected into the valve and the assembly until the seating pressures slightly higher than the process pressure is achieved. The pre-charged accumulator maintains the proper seating pressure over time.
The Quadrosphere is available in sizes 2 to 24 inches and ansi pressure classes to 2500. The valves are manufactured in accordance with industry ball valve standards API 6d and 608. The valves have also been certified to fire safe and fugitive emissions standards.
For more information, contact Automatic Controls of Virginia. Call them at (804) 752-1000 of visit their web site at https://acva.com.
Understanding the Effects of Air in Pipelines
![]() |
Download White Paper Here |
White Paper Courtesy of Val-Matic
The presence of air in a pipeline and its impact on operations is probably one of the most misunderstood phenomena in our industry today. Many operational problems are blamed on inadequate thrust blocking, improper pipeline bedding, etc. These problems include broken pumps, valves and pipe, as well as faulty instrumentation readings. In reality, many of these problems are not caused by improper installation of the equipment but by failure to de-aerate the pipeline. It has been said that if a pipeline is properly de-aerated, you can't guarantee against a line break. However, if you don't properly de-aerate a pipeline, you should be prepared for one.For more information, contact Automatic Controls of Virginia. Visit https://acva.com or call (804) 752-1000.
Automatic Controls of Virginia Salutes Our Veterans
Veterans Day is set aside to honor the men and women who have sacrificed so much in order to serve in the armed forces of the United States.
Veterans Day celebrates and thanks all United States military veterans, alive or dead, and honors the sacrifices that they have made. Our Veterans are our neighbors, friends, family, and co-workers. They took an oath to defend the United States and our Constitution, from all enemies, foreign and domestic. We must never forget their bravery, service, and sacrifice.
Originally called Armistice Day because of the November 11 Armistice that ended World War I, its name was officially changed in the United States in 1954 to Veterans Day to include Veterans of all wars.
Through the observance of Veterans Day, we remind ourselves of our Veterans patriotism, love of country and willingness to serve and sacrifice for the common good.
Automatic Controls of Virginia celebrates and honors America's veterans.
Installation Manual for Waterman Sluice Gate Valves, Fabricated Gate Valves, Drainage Gate Valves, and Specialty Gate Valves

TABLE OF CONTENTS
- Heavy Duty Sluice Gate Installation Instructions
- Medium & Light Duty Sluice Gate Installation Instructions
- Fabricated Slide Gate Installation Instructions
- Drainage (Flap)(tide) Gate Installation Instructions
- Specialty Products Installation Instructions
310 Hill Carter Parkway
Automatic Controls of Virginia: Valve Automation Experts
By combining the industries top electric, pneumatic and hydraulic valve actuators, with its in-house machine shop and fabrication division (Valve Automation Center), Automatic Controls of Virginia has a huge advantage over other valve companies when it comes to design, fabrication, assembly and installation of any valve actuation/automation project. This advantage, along with five decades of hard application experience, makes Automatic Controls an easy choice to be your valve automation partner.
310 Hill Carter Parkway
Suite A
Ashland, VA 23005
Phone: 804-752-1000
Fax: 804-752-1030
https://acva.com
Questtec Solutions Liquid Level Gages and Valves
Questtec Solutions is a company with a long lineage of quality, experience and care in the manufacturing of liquid level gages and valves. The development and engineering of these product lines began more than forty years ago at the former Daniel Level Gage & Valve Company. Today, Questtec Solutions has refined and expanded the Daniel product line to include Magnetic Level gages, High Pressure Steam gages, Electronic Boiler trim and Armored Tubular.
ARMORED REFLEX GAGES
Glass-Trac (formerly Daniel Level Gage & Valve) Reflex Gages are supplied with specially molded glass having prisms on the process side. The purpose of the prisms are to reflect light in the vapor phase of the process. Where the liquid fills the prisms, the display will be nearly black, regardless of the actual color of the liquid.ARMORED TRANSPARENT GAGES
Glass-Trac Transparent Gages use clear, flat glass on both sides of the chamber. Both the color and the interface of liquids can be viewed. Back lighting gage illuminators are available for use with transparent gages to provide enhanced viewing of liquid levels in dimly lit areas.TUBULAR GAGE GLASS ASSEMBLIES
Glass-Trac Tubular Glass Gages are available in any length desired and can be fitted with tubular style gage valves. These gages provide 360° of visibility of the liquid level through strong, clear glass or red line. Guard rods and plastic tubular protectors are available for protectionSEE-LEVEL LED ILLUMINATOR
Illuminator for Transparent Level Gages Certified For Class 1,Division 1, Group B, C, & D Hazardous LocationsFor more information about the Questtec Solutions products, contact Automatic Controls of VA by visiting https://acva.com or by calling (804) 752-1000.
Let Automatic Controls of Virginia Do Your "Valve Automation Heavy Lifting"
Automatic Controls of Virginia has the experience, facilities, and field service capabilities to handle any valve automation project. When it comes to design, fabrication, assembly, and installation, Automatic Controls of Virginia is a solid choice. With five decades of solving some of the toughest valve automation challenges in industrial control and municipal water treatment, Automatic Controls is ready to do the "heavy lifting" with your next valve automation requirement.
Automatic Controls of Virginia
https://acva.com
804-752-1000
Wafer Knife Gate Pinch Valve for the Toughest Slurries and Abrasive Applications
The Flowrox Slurry Wafer Knife Gate Valve (SKW) is designed for heavy duty purposes to isolate flow, even in the most demanding process conditions. The complete valve is built around an ease of maintenance concept and it contains only two service parts: ring sleeves and secondary seal.
- Improved performance - Integrated load distribution ring
- Ease of maintenance - Universal tower design
- Simple installation - One peace body with lockout pins
Bi-directional flow
Bi-directional flow tolerates backflow. 100% isolation.Free flow
Full bore enables free flow of process medium.Wear resistant
Only the ring sleeves in contact with the process medium.Simple to install and service
Face-to-face according to industry standards. Contains only two service parts; ring sleeves and upper seal.Typical installations:
- Tailings slurry lines
- Slurry pump isolation
- Thickener feed and discharge lines
- Flotation isolation
For more information about the Flowrox pinch valves, contact Automatic Controls of VA by visiting https://acva.com or by calling (804) 752-1000.
How EIM Actuators Improve Delayed Coker Operational Uptime
A Refinery’s delayed coking unit is not new technology, but is the most common process to upgrade the residual hydrocarbons remaining after upstream processing to remove water and soluble salts in the crude desalter; production of gasoline, diesel, jet fuel and atmospheric reduced crude through atmospheric distillation; and the production of heavy vacuum gas oil (HVGO) during vacuum distillation. The vacuum reduced crude remaining after these three stages becomes the principal feedstock for the next process stage – delayed coking.
Read this white paper to find out how EIM actuators helped this US refinery improve uptime and reduce cost.
Automatic Controls of VA
(804) 752-1000
https://acva.com
Read this white paper to find out how EIM actuators helped this US refinery improve uptime and reduce cost.
Automatic Controls of VA
(804) 752-1000
https://acva.com
Labels:
EIM,
Maryland,
process control,
refining,
Valve Automation,
Virginia,
Washington D.C.,
West Virginia
Questtec Solutions Liquid Level Measurement Products
- Glass-Trac Liquid Level Gauges and Valves (formally Daniel Level Gauge & Valve)
- Steam-Trac Steam and Water Gauges
- Level-Trac Steam and Water Level Indicators and Alarms
- Magne-Trac Magnetic Gauges
- Armored Tubular
- Sight Flow Indicators
- Guided Wave Radar
- LED Illuminators
- Gauge Valves & Steam Valves
Protecting Drinking Water Pipelines with Inflow Prevention
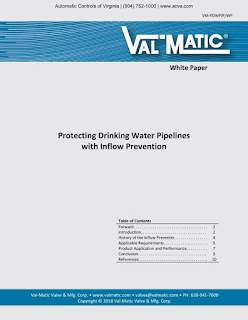
This paper is not intended to provide all of the information necessary for specifying these devices, but rather to explain their function and performance criteria along with common engineering parameters associated with the application of air valves and cross connection control devices. Successful system design should consider the functions of the air valves and vents together with the need to protect the system from contamination and loss of efficiency.
With this knowledge, the design engineer can better apply American Water Works Standard C514 and American Society of Sanitary Engineering (ASSE) Standard 1063 Inflow Preventers and understand the application, sizing, installation guidelines and code applications that affect their use. The rating information provided is based on generally accepted products and standards which offer valuable information for predicting performance.
For more information about the proper application of pressure instrumentation, contact Automatic Controls of VA by visiting https://acva.com or by calling (804) 752-1000.
US Power Grids, Oil and Gas Industries, and Risk of Hacking
A report released in June, from the security firm Dragos, describes a worrisome development by a hacker group named, “Xenotime” and at least two dangerous oil and gas intrusions and ongoing reconnaissance on United States power grids.
Multiple ICS (Industrial Control Sectors) sectors now face the XENOTIME threat; this means individual verticals – such as oil and gas, manufacturing, or electric – cannot ignore threats to other ICS entities because they are not specifically targeted.
The Dragos researchers have termed this threat proliferation as the world’s most dangerous cyberthreat since an event in 2017 where Xenotime had caused a serious operational outage at a crucial site in the Middle East.
The fact that concerns cybersecurity experts the most is that this hacking attack was a malware that chose to target the facility safety processes (SIS – safety instrumentation system).
For example, when temperatures in a reactor increase to an unsafe level, an SIS will automatically start a cooling process or immediately close a valve to prevent a safety accident. The SIS safety stems are both hardware and software that combine to protect facilities from life threatening accidents.
At this point, no one is sure who is behind Xenotime. Russia has been connected to one of the critical infrastructure attacks in the Ukraine. That attack was viewed to be the first hacker related power grid outage.
This is a “Cause for Concern” post that was published by Dragos on June 14, 2019.
“While none of the electric utility targeting events has resulted in a known, successful intrusion into victim organizations to date, the persistent attempts, and expansion in scope is cause for definite concern. XENOTIME has successfully compromised several oil and gas environments which demonstrates its ability to do so in other verticals. Specifically, XENOTIME remains one of only four threats (along with ELECTRUM, Sandworm, and the entities responsible for Stuxnet) to execute a deliberate disruptive or destructive attack.
XENOTIME is the only known entity to specifically target safety instrumented systems (SIS) for disruptive or destructive purposes. Electric utility environments are significantly different from oil and gas operations in several aspects, but electric operations still have safety and protection equipment that could be targeted with similar tradecraft. XENOTIME expressing consistent, direct interest in electric utility operations is a cause for deep concern given this adversary’s willingness to compromise process safety – and thus integrity – to fulfill its mission.
XENOTIME’s expansion to another industry vertical is emblematic of an increasingly hostile industrial threat landscape. Most observed XENOTIME activity focuses on initial information gathering and access operations necessary for follow-on ICS intrusion operations. As seen in long-running state-sponsored intrusions into US, UK, and other electric infrastructure, entities are increasingly interested in the fundamentals of ICS operations and displaying all the hallmarks associated with information and access acquisition necessary to conduct future attacks. While Dragos sees no evidence at this time indicating that XENOTIME (or any other activity group, such as ELECTRUM or ALLANITE) is capable of executing a prolonged disruptive or destructive event on electric utility operations, observed activity strongly signals adversary interest in meeting the prerequisites for doing so.”
Setting the Studs and Nuts Before Mounting a Waterman Fabricated Slide Gate
This video covers how to set up the studs and nuts before mounting a Waterman fabricated sliding gate valve, and also how to adjust the cross rail to ensure there are no gaps between the seat and the slide plate.
INSTRUCTIONS
The first thing you want to do is refer to your submittal drawing to make sure that the studs are exposed to proper length. Align each nut on the corners, so that your gate is perfectly plumb. Go from side to side, and corner to corner, aligning the nuts with the straight edge.
After you have the gate mounted, you'll work with a cross rail seal. Start with the two middle nuts, and alternate one and another, working your way out to the edge of the gate as shown of the Waterman installation manual for fabricated slide gates. Using a 0.004 feeler gauge, check the cross rail seal between the slide and the seal to ensure that it does not pass through. If you do have a place where it crosses through, you need to loosen the front nut and tighten up the back nut, bringing the frame of the gate closer to the slide and decreasing the leakage path.
Go back through the gate installation and make sure all your bolts are very tight, and that you don't have any leakage pass across the top seal. It's the most critical part of your installation - making sure that the cross seal doesn't have any leaks.
ABOUT WATERMAN
Waterman takes pride in their industry-leading technical capabilities and experience. Their engineering knowledge allows them to tackle any project, and they welcome all opportunities to create custom design products for any water control application.
For more information about water control products for water treatment, wastewater, high-volume agricultural and rural surface water delivery, hydro-power, and flood control management, contact Automatic Controls of Virginia. They can be reached by calling (804) 752-1000 of by visiting their website at https://acva.com.
Level Measurement Using Guided Wave Radar
![]() |
Guided wave radar transmitter mounted in bypass chamber with magnetic level gauge. (Questtec Solutions) |
How Do Guided Wave Radar Transmitters Work?
Guided wave radar transmitters rely on microwave pulses. Since microwaves are not affected by dust, pressure, temperature variations, and viscosity, this type of transmitter produces highly accurate results.
A low-energy microwave pulse is sent down a probe, and a part of it is reflected back when the pulse hits the process media. The liquid level is directly proportional to the time-domain reflectometry. The time when the pulse is launched and received back is measured to determine the distance from the surface of the media.
Types of Guided Wave Radar Level Transmitters
Guided wave radar level transmitters are available in different probe configurations. Selecting the right probe is important for successful implementation of the device. While manufacturers offer a range of guided wave radars, most are derived from the three basic probe configurations: single element, twin element, and coaxial.
- Single element probe — The single element probe is the most widely used and least efficient device. The device is popular since it is more resistant to the coating of the liquid.
- Twin element probe — The twin element probe is a good, general purpose probe that is generally used in long-range applications. They are ideal in situations where flexible probes are important for successful reading.
- Coaxial probe — The coaxial probe configuration is the most efficient guided wave radar level transmitters. The probes are used in more challenging low-dielectric applications.
Benefits of Guided Wave Radar Level Transmitters
Guided Wave Radar Level transmitters provide a range of benefits in different applications. The concentration of the measuring signal is strong and clean. This is due to the narrow path of the signal propagation that reduces the chances of impact by stray signals due to obstacles or construction elements inside the tank.
Another benefit of guided wave radar level transmitters is that they are easy to install. No mounting holes are required to install the device. This results in cost savings for the organization. The waveguide can be formed to follow the tank’s contours or mounted at an angle.
The device is ideal in situations where an interface measurement is required. The measuring signals can penetrate the medium deeply, resulting in more accurate results. The waveguide technology is suitable for applications where the medium is subjected to heavy vapors, foam, and dust.
Guided Wave instruments can detect changes in dielectric consents on the boundary of a property. The device can be configured to detect level at both the top and the bottom of a layer of emulsion.
Industrial Application of Guided Wave Radar
Guided wave radar level transmitters are increasingly being used in process industries. The sensors are used in situations that previously employed ultrasonic, hydrostatics, and capacitance. The accuracy specification of the basic model range is up to ±5mm, while the accuracy of the advanced models is up to ±2mm.
The device is generally used in industries to take level readings. The readings are used for local indication and visualization in control systems.
Moreover, guided wave radar level transmitters are also used for managing liquid inventory, determining safety limits, dry run protection, and leak detection. Other applications of guided wave radar level transmitters include communicating low limits to suppliers, automated ordering systems, and streamlining the logistics process.
Guided radar level measurement is also suitable for bulk solids. The surface type is not restricted to liquids since the reflected waves are guided easily through any medium. Foam formation and turbulent liquid surfaces and different angled surfaces (as is the case with bulk solids) don’t influence the accuracy of the reading.
Selection of Guided Wave Radar Level Transmitters
Selection of guided wave radar level transmitters should be based on the requirements of the task. Generally, the rigid single element probe configuration is ideal for angled installations for flowing liquids. The dual flexible wire probe is suitable for most other common applications.
A coaxial probe configuration is recommended for liquids that are cleaner with low dielectric constant and with turbulence on the product’s surface. This type of guided wave radar device is also recommended for installations where the probe is near the tank wall or other obstacles.
Make sure that the device can withstand the range of temperature within the tank. Most GWR devices are rated up to 850 deg F or 450 deg C. You should select a device with added signal strength since this will result in increased reliability and accuracy of the devices.
![]() |
Guided wave radar transmitter. (Questtec Solutions) |
Other factors that should be considered include mounting and proximity. Single probe configuration can be installed almost anywhere. But the single probe configuration can only to apply to specific situations.
Guided Wave radar level transmitters can also be used with an agitator. However, certain things must be considered prior to use the device. The probe must be prevented from contacting the agitator blades. Make sure that you confirm the ability of the probe to withstand the force inside the medium. This is important since turbulent on the surface may decrease the accuracy of the measurement. You can install the device in a bypass chamber or stilling well for an agitated tank. Make sure you speak with an applications expert before specifying or installing a guided wave transmitter. With their consultation, you'll save time as well as improve efficiency and safety.
For more information, contact Automatic Controls of Virginia. Call (804) 752-1000 or visit https://acva.com.
Emerson Bettis CBB Pneumatic Scotch Yoke Actuators: Key Component sand Features
Compact, lightweight and ideally suited for automating ball, butterfly and non- lubricated plug valves, or any quarter-turn (90 degree) rotating mechanism, the CBB Series is also economical and low maintenance. Available in double-acting and spring- return models and are independently certified to IEC 60529 IP66 and IP67M for water ingress protection.
For more information about Bettis actuators, contact Automatic Controls of Virginia by calling (804) 752-1000 or by visiting https://acva.com.
Labels:
Bettis,
CBB,
Emerson,
Maryland,
Scotch Yoke,
Valve Automation,
Virginia,
Washington D.C.,
West Virginia
Automating Large Municipal and Industrial Valves
When you need to automate large ball, butterfly, gate, or globe valves consider Automatic Controls of Virginia.
ACVA has decades of experience, the know-how, the staff, and the facilities to handle the most challenging valve actuation applications.
With scores of successful installations at municipal water facilities, chemical companies, pulp & paper mills and government R&D facilities, ACVA has established a solid reputation for outstanding quality and service.
For more information, contact Automatic Controls of Virginia at https://acva.com or call 804-752-1000.
Magne-Trac Magnetic Level Indicators by Questtec
![]() |
Click for larger view. |

For more information about Questtec Solutions products, contact Automatic Controls of Virginia by calling (804) 752-1000 or by visiting their website at https://acva.com.
XOMOX XP3 and XP 4D: The First Soft Seated Plug Valve Meeting the Most Demanding Emissions Standards
The XOMOX XP3
The XOMOX XP3 Sleeved Plug Valves. with patent pending live loaded cartridge seal, are the first valves to pass all four thermal cycles without any packing adjustments, meeting the ISO 15848-1 standard at the BH BH CO3 200C SSA0.
The XP3 still contains the same maintenance-free and cavity-less design benefits of the standard XOMOX® sleeve plug valve, namely no costly lubrication required and no accumulation or contamination of process media.
The XOMOX® XP 4D
The XOMOX® XP 4D Sleeved Plug Valve contains the same live loaded stem cartridge as XP3, while also adding a set of contingency bolting. This additional set of packing allows for a manual override of the seal to atmosphere manual adjustable 4D stem seal of the cover. If there is any emergency failure, this seal can be activated and reduce the need (in the very unlikely case) of any costly unscheduled shutdowns.
XP 4D Features:
- Primary Seal to Atmosphere - Sleeve ensures inline sealing. Manual adjustments are possible.
- Tertiary Seal to Atmosphere Additional 4D Manual - Live loaded cartridge provides improve stem sealing.
- Additional 4D Manual - Manual 4D stem packing for adjustment in case of emergency or excessive assurance.
Technology Demo: Emerson EIM Electric Actuators for Valves, Dampers, and Louvers
EIM is known for its innovative electric valve actuators built for the harshest industrial and municipal applications. You'll find EIM actuators throughout the processing industries, where reliability is critical - oil and gas, power, refining, chemical, petrochemical, water/wastewater and mining. EIM actuators and controls have a proven track record for performance in critical shutdown applications.
EIM offers a wide range of electric actuators with different frame sizes, horsepower ratings and output speeds readily tailored to your specific applications. EIM electric actuator products are selected by application requirements of voltage, torque, operating time, and valve shaft diameter. Actuators are designed tor ball, plug, and butterfly valves as well as quarter turn damper and louver drives.
For more information in the Commonwealth of Virginia, Washington D.C. and Maryland, contact:
(804) 752-1000
Industrial Pinch Valve Operation and Performance
A pinch valve offers a cost-effective and practical solution for controlling the flow of media through a pipe line or any other system. The operating principle of pinch valves is simple. In the open position, the valve is full bore with no flow restrictions. During closing, two pinch bars squeeze the valve sleeve shut on the centerline. The sleeve is naturally wear resistant and when particles hit the sleeve’s rubber surface, the energy is absorbed and released when the rubber bounces back.
Pinch valves are controlled through linear motion via a manual screw mechanism, or linear pneumatic or electric actuator.
Heavy duty pinch valves provide bubble tight shut-off even if solids have built up on the sleeve wall. When compressed, any crystallized particles flake-off the sleeve surface. The full bore structure ensures free flow of the medium. The construction and materials of the three main components (sleeve, body and actuator) can be tailored to suit your process conditions.
Pinch valves have gained increased popularity in a wide variety of industries such as waste water treatment, cements, mining, food and beverage, medical, pharmaceuticals, others, primarily because they offer tight shut-off, full bore flow, and pressurized self-cleaning from the movement of the flowing media.
Benefits of pinch valves:
- Long service intervals.
- Only one wearing part.
- Excellent for slurries, dry powders, and abrasive materials.
- Low maintenance cost.
www.acva.com
(804) 752-1000
Labels:
abrasive,
Floxrox,
Maryland,
pinch valve,
slurries,
Virginia,
Washington D.C.,
Wastewater,
West Virginia
American Water Works Association Valve Standards and Descriptions
The American Water Works Association (AWWA), the leading non-profit, scientific and educational association dedicated to water management and treatment. AWWA members include water utilities, treatment plant operators and managers, and manufacturers. The AWWA maintains and regulates the design and performance standards of valves and actuators used in municipal water treatment and distribution systems. The following are the standards with links for additional information:
This standard describes the double check valve back flow prevention assembly. The assembly shall be for operation on hot or cold water lines and capable of withstanding a working water pressure of at least 150 psi (1,034 kPa) without damage to working parts or impairment of function. This standard describes hot- and cold-water double check valve back flow prevention assemblies. Assemblies shall be designed to operate at a minimum temperature range of 33ºF to 140ºF (1ºC to 60ºC). Hot water assemblies shall be designed to operate, at a minimum, in water at a temperature range of 33ºF to 180ºF (1ºC to 82ºC). A complete assembly consists of two internally loaded, independently operating check valves, located between two tightly closing resilient-seated shutoff valves, with four properly placed resilient-seated test cocks (see Sec. 4.3.1.3). Major revisions made to the standard in this revision include the following: AWWA standard materials statement has been added (Sec. III.A.2 and Sec. 4.1); synthetic coating of ferrous bodies has been removed (Sec. 4.1.2); the material callouts have been updated (Sec. 4.1.3); the identification of nominal size of the assembly has been revised (4.2.1.1); the requirements for structural capability and operational capability have been revised (Sec. 4.2.2.1 and Sec. 4.2.2.2); the sections on area of waterways, clearance of moving parts, facing rings for poppet-type valves, facing rings for swing-type valves, and bushings have been removed (former Sec. 4.3.1.2 through Sec. 4.3.1.6); the requirements for shutoff valves have been updated (Sec. 4.3.1.6); requirements for operational cycle testing have been added (Sec. 4.3.2.3); and, requirements for replacement parts have been added (Sec. 4.3.4).
This standard establishes minimum requirements for rubber-seated butterfly valves, 3 in. (75 mm) through 72 in. (1,800 mm) in diameter, with various body and end types, for fresh water having a pH range from 6-12 and a temperature range from 33º-125ºF (0.6º-52ºC). This standard covers rubber-seated butterfly valves suitable for a maximum steady-state fluid working pressure of 250 psig (1,723 kPa), a maximum steady-state differential pressure of 250 psi (1,723 kPa), and a maximum fully open fluid velocity of 16 ft/sec (4.9 m/sec) based on nominal valve size. The major revisions made to the standard in this edition include the following: permeation language was moved to the Foreword under Special Issues, Sec. II.C; and, new requirements were provided for mechanical-joint-end valves.
AWWA C500-09 Metal-Seated Gate Valves for Water Supply Service
This standard describes iron-body, brass-mounted, non-rising stem (NRS) gate valves, including tapping gate valves, 3-in. (75-mm) NPS through 48-in. (1,200-mm) NPS, and outside screw and yoke (OS&Y) rising-stem gate valves, 3-in. (75-mm) NPS through 24-in. (600-mm) NPS, with either double-disc gates having parallel or inclined seats, or solid-wedge gates. These valves are suitable for use in approximately level settings in water systems. These valves are intended for applications where fluid velocities do not exceed 16 ft/sec (4.9 m/sec) when the valve is in the fully open position. The major revisions in this edition of ANSI/AWWA C500 include the following: editorial changes to conform to current AWWA form and content; permitting the use of stainless-steel stems and reduced-thickness ductile-iron flanges; addition of stainless steel as a stem material; addition of a "non-integral thrust collar" for stems in NRS valves; addition of aluminum-bronze and silicon-bronze copper alloys; provision for reduced flange thickness for end flanges of ductile-iron flanged valves; addition of 14-in. and 18-in. valve sizes; and, addition of metric fasteners and socket head fasteners.
AWWA C510-07 Double Check Valve Backflow Prevention Assembly
This standard describes the double check valve back flow prevention assembly. The assembly shall be for operation on hot or cold water lines and capable of withstanding a working water pressure of at least 150 psi (1,034 kPa) without damage to working parts or impairment of function. This standard describes hot- and cold-water double check valve back flow prevention assemblies. Assemblies shall be designed to operate at a minimum temperature range of 33ºF to 140ºF (1ºC to 60ºC). Hot water assemblies shall be designed to operate, at a minimum, in water at a temperature range of 33ºF to 180ºF (1ºC to 82ºC). A complete assembly consists of two internally loaded, independently operating check valves, located between two tightly closing resilient-seated shutoff valves, with four properly placed resilient-seated test cocks (see Sec. 4.3.1.3). Major revisions made to the standard in this revision include the following: AWWA standard materials statement has been added (Sec. III.A.2 and Sec. 4.1); synthetic coating of ferrous bodies has been removed (Sec. 4.1.2); the material callouts have been updated (Sec. 4.1.3); the identification of nominal size of the assembly has been revised (4.2.1.1); the requirements for structural capability and operational capability have been revised (Sec. 4.2.2.1 and Sec. 4.2.2.2); the sections on area of waterways, clearance of moving parts, facing rings for poppet-type valves, facing rings for swing-type valves, and bushings have been removed (former Sec. 4.3.1.2 through Sec. 4.3.1.6); the requirements for shutoff valves have been updated (Sec. 4.3.1.6); requirements for operational cycle testing have been added (Sec. 4.3.2.3); and, requirements for replacement parts have been added (Sec. 4.3.4).AWWA C507-11 Ball Valves, 6 in. through 60 in. (150 mm through 1,500 mm)
This standard covers gray-iron, ductile-iron, and cast-steel, flanged-end, low-leakage, shaft- or trunnion-mounted, full-port, double- and single-seated ball valves for pressures up to 150 psi (1,050 kPa) in sizes 6-in. through 60-in. (150-mm through 1,500-mm) diameter and pressures up to 300 psi (2,100 kPa) in sizes from 6-in. through 48-in. (150-mm through 1,200-mm) diameter for use in water, wastewater, and reclaimed water systems having water with a pH greater than 6 and less than 12 and with temperatures greater than 32ºF (0ºC) and less than 125ºF (52ºC). Design fluid velocity - the valve assembly shall be structurally suitable for a port fluid velocity of 35 ft/sec (10.7 m/sec) at design pressure and shall be within the allowable stresses noted in Sec. 4.3.1. Pressure class and rated/design pressure - the classes of valves discussed in this standard shall be designed for the maximum rated pressure. Rated pressure is defined as the design pressure at 100ºF (38ºC). The major changes made in this revision of the standard include the following: added sizes 54 in. and 60 in. (1,350 mm and 1,500 mm); added paragraph 25 in Section III regarding the consideration of requiring pulls less than 80 lb (356 N) for hand-wheels and chainwheels; added paragraphs 1.4 on Valve Construction and 1.5 on Description of Operation to Sec. 1, General; revised Table 1 in Sec. 4.3, Port diameter and minimum body shell thickness, to require that the wall thicknesses of ductile-iron construction be the same wall thicknesses as cast steel construction; added paragraph 4.3.9.4 on design methodology for the valve shafts; revised the metal-seat leakage requirements in Sec. 5.1.2.3; revised coating requirements in Sec. 4.4.3; added actuator pressure rating and actuator flow rating to nameplate requirements; and, added Appendix A on Installation, Operation, and Maintenance of Ball Valves.AWWA C509-09 Resilient-Seated Gate Valves for Water Supply Service
This standard describes iron-body, resilient-seated gate valves with non-rising stems (NRS) and outside screw-and-yoke (OS&Y) rising stems, including tapping gate valves, for water supply service having a temperature range of 33º-125ºF (0.6º- 52ºC). These valves are intended for applications where fluid velocity does not exceed 16 ft/sec when the valve is in full open position. Major revisions made to the standard in this edition include the following: editorial changes to conform to current AWWA form and content; addition of reduced-thickness ductile-iron flanges; addition of stainless-steel alloys for use as a stem material; permitting the use of non-integral thrust collars for stems in NRS valves; addition of aluminum-bronze and silicon-bronze copper alloys; addition of 14-, 18-, and 36-in. valve sizes; addition of socket head and metric fasteners; requirement to use an anti-seize compound with stainless-steel bolts and nuts; and, removal of maximum phosphorus content.AWWA C515-09 Reduced-Wall, Resilient-Seated Gate Valves for Water Supply Service
This standard describes reduced-wall, resilient-seated gate valves with non-rising stems (NRS) and outside screw-and-yoke (OS&Y) rising stems, including tapping gate valves, for water supply service having a temperature range of 33º to 125ºF (0.6º to 52ºC). These valves are intended for applications where fluid velocity does not exceed 16 ft/sec (4.9 m/sec) when the valve is in the fully open position. Major revisions made to the standard in this edition include the following: revised to cover 42-in. NPS and 48-in. NPS sizes; revised to include integral and non-integral thrust collar stem designs; revised to include reduced flange thickness for flanged-end valves; revised to include socket head and metric fasteners; added additional copper alloys to Table 5; and, revised to include the use of stainless-steel components (Sec. 4.2.3.5).
AWWA C504-10 Rubber-Seated Butterfly Valves, 3 In. (75 mm) through 72 In. (1,800 mm)
This standard establishes minimum requirements for rubber-seated butterfly valves, 3 in. (75 mm) through 72 in. (1,800 mm) in diameter, with various body and end types, for fresh water having a pH range from 6-12 and a temperature range from 33º-125ºF (0.6º-52ºC). This standard covers rubber-seated butterfly valves suitable for a maximum steady-state fluid working pressure of 250 psig (1,723 kPa), a maximum steady-state differential pressure of 250 psi (1,723 kPa), and a maximum fully open fluid velocity of 16 ft/sec (4.9 m/sec) based on nominal valve size. The major revisions made to the standard in this edition include the following: permeation language was moved to the Foreword under Special Issues, Sec. II.C; and, new requirements were provided for mechanical-joint-end valves.AWWA C542-09 Electric Motor Actuators for Valves and Slide Gates
This standard describes electric motor actuators for valves and slide gates in water, wastewater, and reclaimed water utility systems. Electric motor actuators are designed to produce a multi-turn rotary motion output to actuate a multi-turn valve or gate, or to actuate an external gear head for quarter-turn valves. Electric motor actuators not requiring external gear heads for quarter-turn valves are defined in Sec. 4.4.1.2. This is the first edition of this standard, and therefore, there are no revisions.AWWA C508-09 Swing-Check Valves for Waterworks Service, 2-In. through 24-In. (50-mm through 600-mm) NPS
This standard describes only iron body, non-assisted, swing-check valves, 2-in. through 24-in. (50-mm through 600-mm) NPS, with mechanical-joint or flanged ends that are installed in approximately level settings in water systems. The manufacturer should be consulted for special conditions. Check valve sizes described in this standard are 2-, 2 1/2-, 3-, 4-, 6-, 8-, 10-, 12-, 14-, 16-, 18-, 20-, and 24-in. (50-, 65-, 75-, 100-, 150-, 200-, 250-, 300-, 350-, 400-, 450-, 500-, and 600-mm) NPS. Sizes refer to the nominal diameter of the waterway through the inlet and outlet connections and the seat ring. Major revisions made to the standard in this edition include the following: the pressure ratings were revised in Sec. 1.1.4; standard end-to-end dimensions were moved from the appendix to the body of the standard in Sec. 4.4.2 and Table 2; new ductile-iron flange thicknesses were added to Sec. 4.4.7.1 and Table 3; and, a new appendix titled "Installation, Operation, and Maintenance of Swing- Check Valves for Waterworks Service" was added.AWWA C512-07 Air-Release, Air/Vacuum, and Combination Air Valves for Waterworks Service
This standard describes 1/2 in. (13-mm) through 6 in. (150-mm) air-release valves and 1/2 in. (13-mm) through 20-in. (500-mm) air/vacuum and combination air valves having gray cast-iron or ductile-iron bodies and covers. The valves are designed for use in water systems with maximum working pressures of 300 psig (2,070 kPa [gauge]) and water temperatures ranging from above freezing to a maximum of 125ºF (52ºC). Major changes made to the standard in this revision include the following: added requirements for throttling devices in Sec. 4.3.3; and, added requirements for slow-closing devices in Sec. 4.3.4.AWWA C517-09 Resilient-Seated Cast-Iron Eccentric Plug Valves
This standard describes resilient-seated cast-iron eccentric plug valves, 3 in. (75 mm) through 72 in. (1,800 mm) in diameter, with flanged, grooved, or mechanical-joint ends, for water, wastewater, and reclaimed water systems having a pH range from 6 to 12 and a temperature range from 33ºF to 125ºF (0.6ºC to 52ºC). The minimum design pressure shall be 175 psig (1,208 kPa) for 3 in. through 12 in. (75 mm through 300 mm) sizes and 150 psig (1,034 kPa) for 14 in. through 72 in. (350 mm through 1,800 mm) sizes. Major changes made to the standard in this revision include the following: expanded Scope and Purpose to include wastewater and reclaimed water service; added references to ANSI/AWWA Standards C541 and C542 for power actuator requirements; and, removed contractual language from the body of the standard.AWWA C541-08 Hydraulic and Pneumatic Cylinder and Vane-Type Actuators for Valves and Slide Gates
This standard describes hydraulic and pneumatic cylinder and vane-type actuators for operation of valve and slide gates in utility systems. This is the first edition of this standard, and therefore, there are no revisions.Pinch Valves and Knife Gate Valves for Abrasive and Slurry Service
![]() |
Flowrox pinch valve. |
Flowrox heavy duty pinch valves and knife gate valves are made to last and are ideal where shut-off and control applications involve abrasive or corrosive slurries, powders or coarse substances.
![]() |
Flowrox knife gate valve. |
The designs of Flowrox Slurry Knife Gate Valves are based on the years of experience Flowrox has gained, providing reliable solutions for abrasive and corrosive process applications. They feature a load distribution ring that prevents over compression and ensures tight sealing between the sleeve and the valve gate.
For more information, contact Automatic Controls of Virginia. Call them at (804) 752-1000 or visit them at https://acva.com.
Side-by-Side Comparison of Swing Check Valves and Resulting Mechanical Shock Caused by Reverse Flow
Swing check valve mechanical shock (slam) is caused by the sudden build-up of reverse flow after a pump has stopped, being followed by the sudden stoppage of that reverse flow by the check valve. The faster the check valve closes the less reverse flow, and hence the smaller slam. This video (courtesy of Val-Matic) demonstrates this phenomenon under real operating conditions.
Automatic Controls of VA
https://acva.com
(804) 752-1000
Automatic Controls of VA
https://acva.com
(804) 752-1000
Automatic Controls Industrial Valve, Automation & Control Blog
We're building this blog to provide people interested involved with industrial valves, valve automation, instrumentation and control a place to learn interesting applications, products, and basic knowledge.
The markets we serve are the municipal water and wastewater treatment, environmental and industrial companies located in Virginia, North Carolina, West Virginia and Southern Maryland.
We'll do our best to provide weekly posts to keep the blog fresh and informative, and a place you'll want to check back with regularly.
The markets we serve are the municipal water and wastewater treatment, environmental and industrial companies located in Virginia, North Carolina, West Virginia and Southern Maryland.
We'll do our best to provide weekly posts to keep the blog fresh and informative, and a place you'll want to check back with regularly.
Labels:
Control,
Flow,
Instrumentation,
Maryland,
Municipal,
North Carolina,
Treatment,
Valve Automation,
Valves,
Virginia,
Wastewater,
Water,
West Virginia
Subscribe to:
Posts (Atom)